A Report on 9th International Workshop on Crystallization , Filtration and Drying
By
Poonam Vij , Research Associate,
Institute of Chemical Technology (ICT),
Matunga (E), Mumbai 400019
Email: vijpoonam@gmail.com
The World Forum for Crystallization, Filtration and Drying, had its 9th year of the forum from 26th to 28th February, 2015. The theme of this year’s event was Drying and Granulation Technology. The event was conducted at the K.V.Auditorium at Institute of Chemical Technology.
Just like the previous events, the 9th WFCFD conference provided a range of talks from both industry and academia and an overview of the present advancements in the themed fields of Drying and Granulation. A platform where the experts shared, discussed ideas and also established new collaborations.
The event was spread across three days, including lectures by experts on the ProCell Lab (Granulation equipment by Glatt). There was an extensive Q&A session with the makers of this latest granulation technology.
In current market scenario, granulation is one of the most important manufacturing processes in pharma and food industry. The Technologies and equipment discussed were especially for cost minimization and scale-up projects aspects. Drying technology now plays an important role in the urban and rural society by contributing to sustainability and environment in various ways.
The Workshop was attended by 100 odd delegates from leading companies in India as well as overseas. Some of the companies were Glatt (Germany), The Fitzpatrick Company (USA), Reliance Industries Ltd., United Phosphorus Ltd., Tata Chemical Ltd. and many more.
The Chief Guest, Vice-chancellor of Institute of Chemical Technology (ICT), Prof. G.D.Yadav, inaugurated the workshop by giving the speech on the achievements, ambitions and future goals set forth by chemical engineers and technologists for the betterment of the society. Sustainable growth of chemical industry is only possible through the innovation in several areas including pharmaceutical and food industries. He highlighted the role of chemical engineers and biotechnologists who have contributed immensely to the development of new generation medicines, nano and bio-pharmaceuticals. The workshop started with a plenary talk by Dr. Sanjeev Katti, Senior Vice-president, Research and Technology, Reliance Technology Group. Dr Katti spoke on the need to develop smart technologies in the area of powder and particle handling, in particular, crystallization, robust filtration equipment with minimum downtime and high efficiency of S/L separation. He emphasized the need of granulation on non-pharma application to convert powdery mass into free flowing granules for dust-free properties and ease of handling.
Professor B. N. Thorat, the founder president of World Forum for Crystallization, Filtration and Drying (WFCFD) and Professor of Chemical Engineering at ICT, discussed about the fundamentals of drying technology. How vital is the characteristics of the wet as well as dry material, he stressed upon determination of basic drying kinetics and the measuring desorption and adsorption moisture isotherm under varying temperature conditions. Selecting the right drying system is important keeping in view the pre and post drying operations, which influenced the selection of the right dryer. The classification of dryers based on solids handling, efficient heat transfer, batch and continuous plant integrity were discussed in length.
The second lecture was presented by Mr. Sangeet Bagaria, TeaKraft from Coimbatore. The topic for his presentation was ‘Sun drying to Mechanized drying’. Mr Bagaria gave an overview of both methods along with a comparative analysis. Different Mechanised dryers such as Vibro-Fluidized Bed dryer, Multi Pass Conveyor Dryer etc. were detailed. M/s. Teacraft, a leading manufacturer of dryers in India showcased various drying systems designed for handling of variety of materials including food materials, pigments and specialty products. The continuous dryer based on pre-formed materials such as mica and variety of pigments was the highlight of his lecture.
Prof. Meng Wai Woo from Monash University, Australia, focused on spray drying and functional particles for the food and pharmaceutical industry. He also undertakes computational fluid dynamics (CFD) research with application to manufacturing systems and provides industrial consultation in this area. The first lecture by Dr. Woo was on ‘Antisolvent vapour precipitation of particles’. The talk discussed about the dependence of spray dried solid particle size over initial droplet size and the use of antisolvent for absorption and precipitation of ultrafine particles followed by dehydration to obtain dried ultrafine particles. The second lecture by Dr. Woo was on ‘CFD Simulations of Spray Dryers’, which accounted for detailed geometrical factors, chaotic and random conditions within the chamber, minimal assumptions on the key phenomenon and using various models for prediction of core air flow.
The next talk was presented by Mr. P.B.Kulkarni from Litel Infrared Systems Pvt. Ltd. Mr. Kulkarni began his presentation titled “Industrial Applications of Infrared. Principles and practices” with a brief introduction about Litel and stated that Litel introduced indigenous infrared heating technology in India. Litel was described as a solutions company that provides standard and customized solutions for various industries viz Powder curing, Glass printing, Thermo forming, Coil coating and many more. The objective of the talk was to review the basic principles of Infra Red (IR) technology, Application of IR in surface and bulk heating/drying and other benefits involving energy efficiency. Mr. Kulkarni gave an overview of basic laws of infrared and their significance to the industry by displaying some practical examples such as in aerospace application; IR is used at 5MW/m2 to raise temperatures to 1600 degree Celsius in a matter of seconds. The benefits experienced by industry are such as very short time cycles; typical convection process time reduction to 1/3rd in case of surface coating and in some cases time is reduced from 10 days to 2 hours as well. IR can provide uniform heating even if materials are non conductive. It is user friendly and safe. Hence Mr. Kulkarni then summarised the benefits of IR in terms of energy, quality, time and throughput, and IR can provide clean operation and suitable post harvest operation in pharma industries.
Going forward, we had Mr Shripad Khatav who emphasised on importance Zero Liquid Discharge (ZLD) by use of Multiple Effect Evaporators. It has become mandatory that the industries should recover unreacted raw materials from the waste stream, using strippers. The segregation of waste into high TDS stream and high boiling organics may turn out to be beneficial for achieving zero liquid discharge. This is particularly true in case of Pharmaceutical and fine chemical industries, who are mandated to achieve zero discharge norms in coming years. This is particularly true in case of these industries located in land locked regions of MIDC. He showcased several examples where by the condensate coming out of MEE can be reclaimed are reused partially or totally depending on the complexities involved in the mixed stream.
The second day began by welcoming Prof. Xiao Dong Chen, from Soochou University, China. Prof. Chen has published over 440 refereed journal articles and 220 conference papers. Professor Dong Chen was honored with “Professor Arun S. Mujumdar distinguished Visiting Professor” for year 2014-2015. With Prof. Dong Chen’s first talk was on ‘Chemical Process engineering Innovations’ which explained different techniques used to detect different particle sizes. In his further lectures, Prof Chen detailed on ‘Fouling and Cleaning’. The areas covered here were different types of Fouling especially Biofouling case studies of Dairy Fouling and OVA protein fouling and its corresponding cleaning techniques. It also mentioned about modeling the Heat transfer and fouling layer growth kinetics, reduction of Fouling using Chemical Additives, surface charges and high velocity. Prof Chen also described the types of Anti fouling coatings such as Chemically Active Antifouling Coatings, Nontoxic Coatings and biodegradable coatings and their applications in different conditions. Prof Chen proceeded on the third day focusing on ‘Spray drying’. Using MDSD – Powder Design and Development Tool, Puffing at different temperatures and Wettability of Particles accompanied with CFD of particles of spray drying were covered. In continuation to the topic, Prof Chen introduced Modeling Drying by Reaction Engineering Approach. He concluded by stating that Multi-scale Modeling along with Multi-scale Experimentation is the way to go.
The second lecture was presented by Dr. Kyuya Nakagawa from Kyoto University, Japan. Dr. Kyuya Nakagawa is an Associate Professor at the Division of Food Science and Biotechnology at Kyoto University. He is interested in the development of food processing technology that allows designing desirable structures in food products to give functionalities. Freezing and drying, he recognizes them as a great tool to process structured materials. Dr. Nakagawa presented two talks. The first talk was on ‘Fundamentals of Freeze Drying - modeling, case studies for practical application’. Dr.Nakagawa started the talk explain the fundamentals of freeze drying by covering various stages such as coolong, super cooling, nucleation, ice crystal growth, eutectic Phase separation and then thr drying steps which involve ice sublimation, desorption and finally the Freeze Dried product. How freeze dried components along with conductive chilling process and finally convective chilling lead to a freeze dried product was discussed. Dr. Nakagawa stated that Freezing makes an ice microstructure in a solution when the velocity of freezing is maintained at a certain value. Later laying down the factors such as pH variation, phase separation etc, Dr Nakagawa covered the factors that may cause sensitive protein denaturation during freezing. Further in the lecture, we understood that drying time minimization is achieved if increasing product temp by monitoring product temperature, improving mass and heat flow and the Ice morphologies, which involve controlled freezing and annealing. The quality of dried products can be controlled using excipients, which avoid collapse as well as physiochemical changes in the drying. Controlled freezing and drying by creating homogeneity in freeing and rapidity also leads to better product. Finally stability of sensitive ingredients can be maintained using excipients and by reducing stress due to freezing, dehydration and thermal stress on the product. The rest of the lecture focused on Mass balance in a freeze dryer, Heat input by radiation, Heat input by Conduction, Mass flow in a product, Mass flow in a Dryer and Ice sublimation test results. A case study using Freeze dried apples was demonstrated. The second talk was on ‘Application of Freeze Drying on protein based encapsulation’. Ageing, Microencapsulation, Dehydration and Rehydration of proteins were explained using various case studies.
Dr. Michael Jacob is Technical Director and member of the General Management of Glatt Ingenieurtechnik GmbH in Weimar, Germany. M/s. Glatt has plant engineering competence in innovative granulation process technology. His main working fields are particle technology, fluidized beds, and application & technology development. Dr Jacob presented a lecture over video conferencing on ‘Fluidised Bed and Spouted Bed Granulation process’. The lecture mentioned Fluidised Bed basics, Processing Options like Spray Granulation, agglomeration, particle formation; Types of Granulation equipments; and an overview of Laboratory units and Pilot Plants.
Mr Volker Budzinski, GLATT, presented the demonstration of the working model of the PROCELL Lab System, which is to be installed at Professor Thorat’s lab in Institute of Chemical Technology. The details covered included the Use, Technical Data, Processing Options, Modular concept, Layout & Main Components, Process Inserts and Control Systems. The first part involved uses of the system such as the Pro Cell being a lab allrounder for the evaluation of fluid bed and spouted bed process in one single unit and capable of continuous or batch operation. Using inserts for spray granulation, agglomeration, coating, encapsulation, powder layering and cooling/drying, the ProCell can do feasibility tests and product development. The system can be process air or nitrogen operated and can produce a small batch from 500g to 10 kgs. Mr Budzinski showcased the technical data sheet and how various inserts can be used for conducting their designed processes. Processing operations were divided in three parts – spouted bed, fluidized bed and rotor. The modular concept of the ProCell Lab System exercises three processes, which involve performance, exhaust treatment and spraying system. The salient features of the Lab system and its impressive design along with the advanced explosion protection were perfect for our industry audience.
Mr. Michael Prior from The Fitzpatrick Company, graduated in Chemical Engineering from The University of Manchester UK in 1971, is a Fellow of the Institution of Chemical Engineers. He has worked in the powder processing industry for over 40 years, specializing in agglomeration, compaction, size reduction, air classification, and powder mixing. His talk title was ‘Lean Pharma Manufacturing Using Roll Compaction’. Resources should only create value and eliminate waste such that the manufacturing is efficient. Lean Manufacturing focuses on value based on user requirements, continuous optimized flow and flexible equipment creating Pull production. Granulation is one of the key components in pharmaceutical world. The requirements of granulation are such that it should Predict flow and uniformity of the mix, maintain drug properties, compose of uniform drug dose in each tablet, provide sufficient cohesive properties to form firm tablet under compression, have lubricant properties which prevent binding of tablets and the ability to operate at high speed production equipment.
Mr. Prior advanced by discussing advantages of Dry Granulation over Wet granulation, Details of Roll Compaction Dry Granulator and to maintain various parameters while designing roll Compactors. Wet granulation process steps and advantages such as uniform dispersion and duplication of colors, disadvantages such as high manufacturing capita costs, material loss, cross contamination chances were all laid out my Mr. Prior. Further Mr. Prior explained dry granulation using roll compaction is done by blending drug formulation, feeding the material to compression rolls and creating final product and blending the ingredients such as lubricant. Direct Compression and its advantages and disadvantages were laid. Mr. prior stated that various materials are blended together prior to tableting. The API and excipients must exhibit the material characteristics required for processing by tablet press. Further Mr. Prior elucidated the Roll Compaction is Lean as compaction is well established and used method of granulation in pharma industry, there are significant benefits with dry granulation and the state of the art machines meet pharma standards. Further the audience was given insights on the CCS Series Chilsonators which is a Contained Compaction System manufactured by The Fitzpatrick Company. The variables affecting compaction were compared with the Process Efficiency, Versitality and uniform Quality of the Chilsonator. Further the cGMP features and containment features were discussed. The lecture was hence concluded by stating that Roll compaction saves cost-Lean, it is simple and reliable, contained, scalable and it is the first choice of many.
MS. POONAM VIJ
DEPARTMENT OF CHEMICAL ENGINEERING
INSTITUTE OF CHEMICAL TECHNOLOGY
MUMBAI.
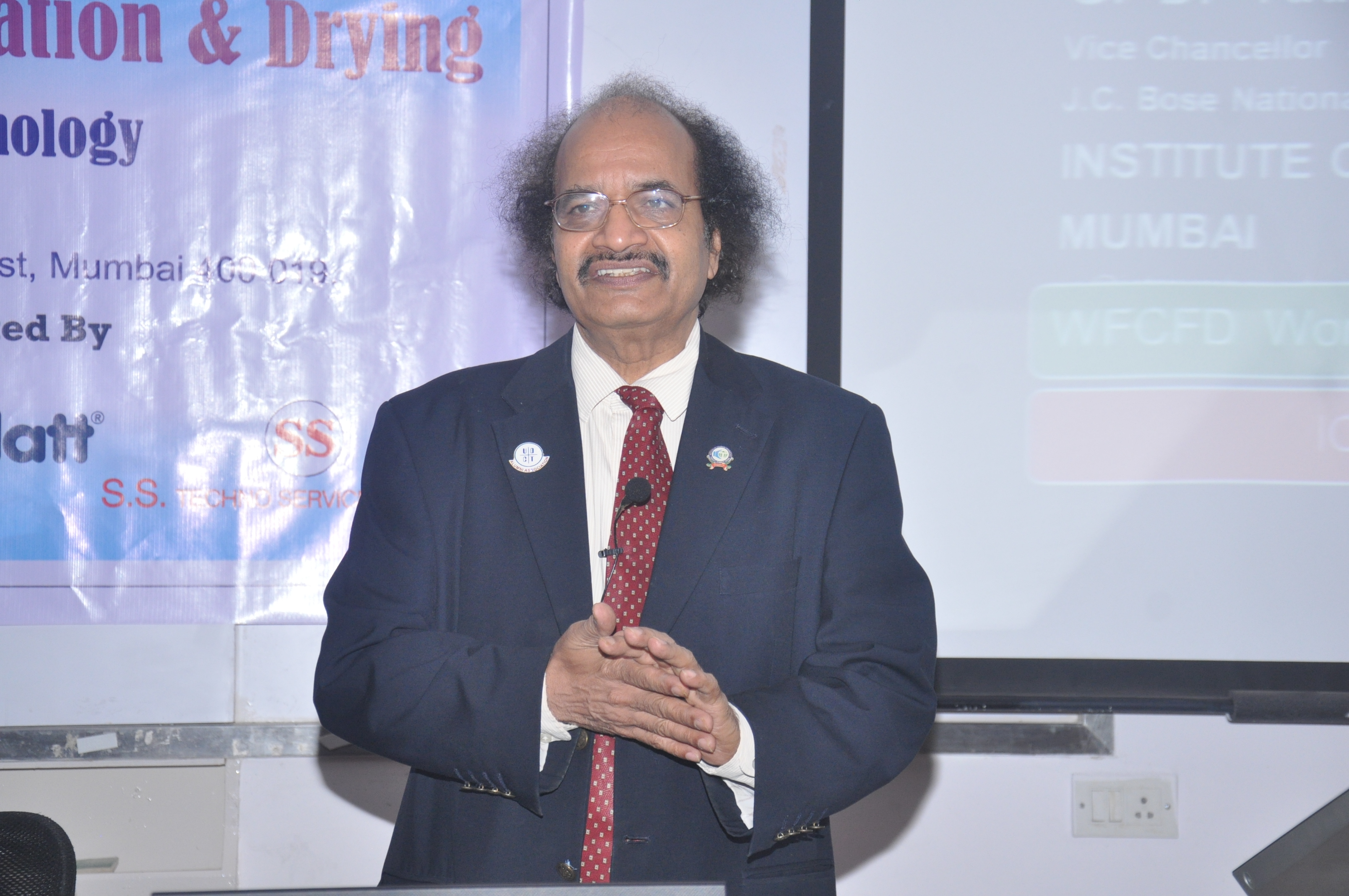
(Prof. G.D.Yadav, Vice Chancellor, Institute of Chemical Technology)
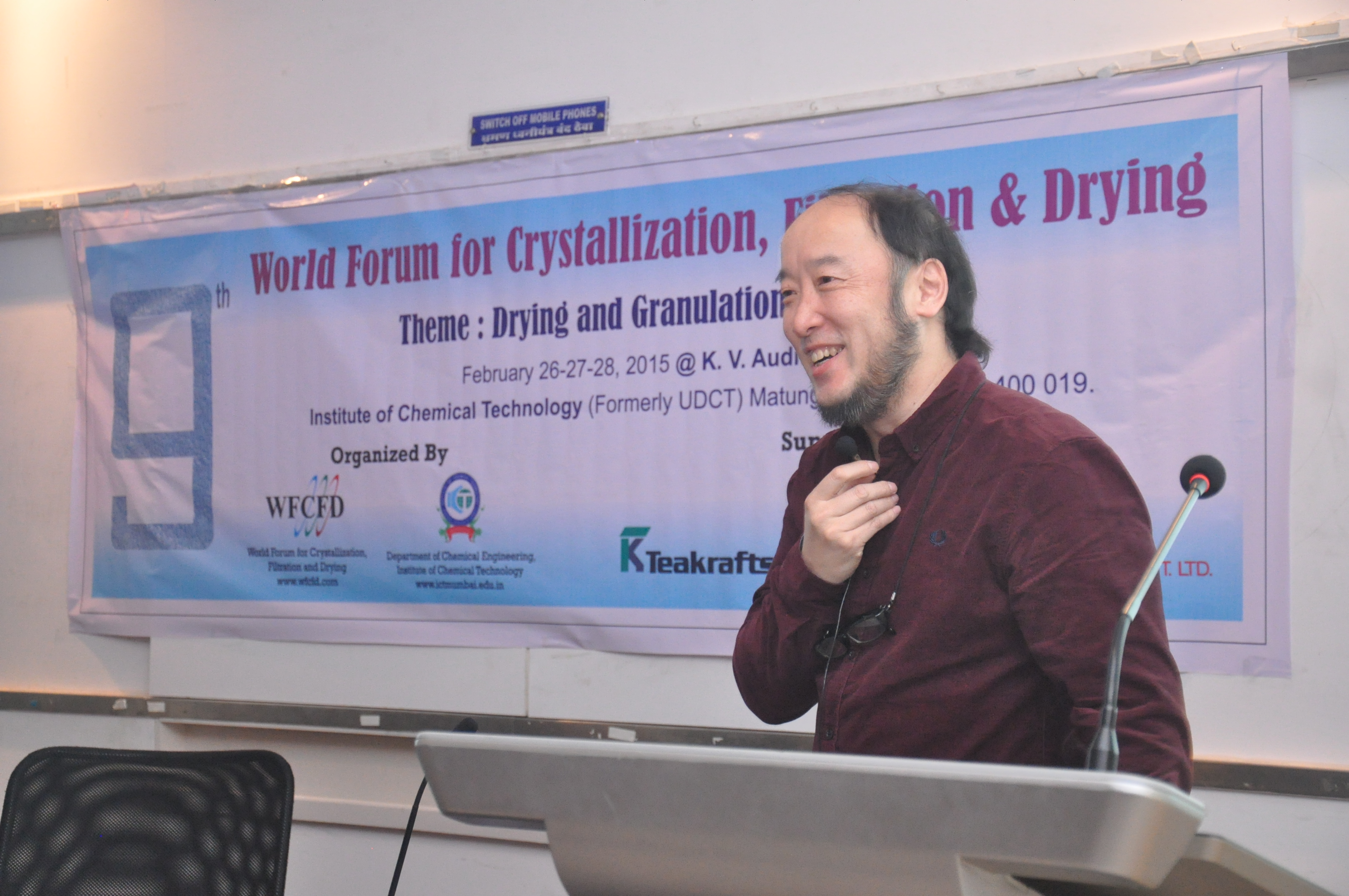
(Prof. Xiao Dong Chen, Monash University, Australia and Soochow University, China)
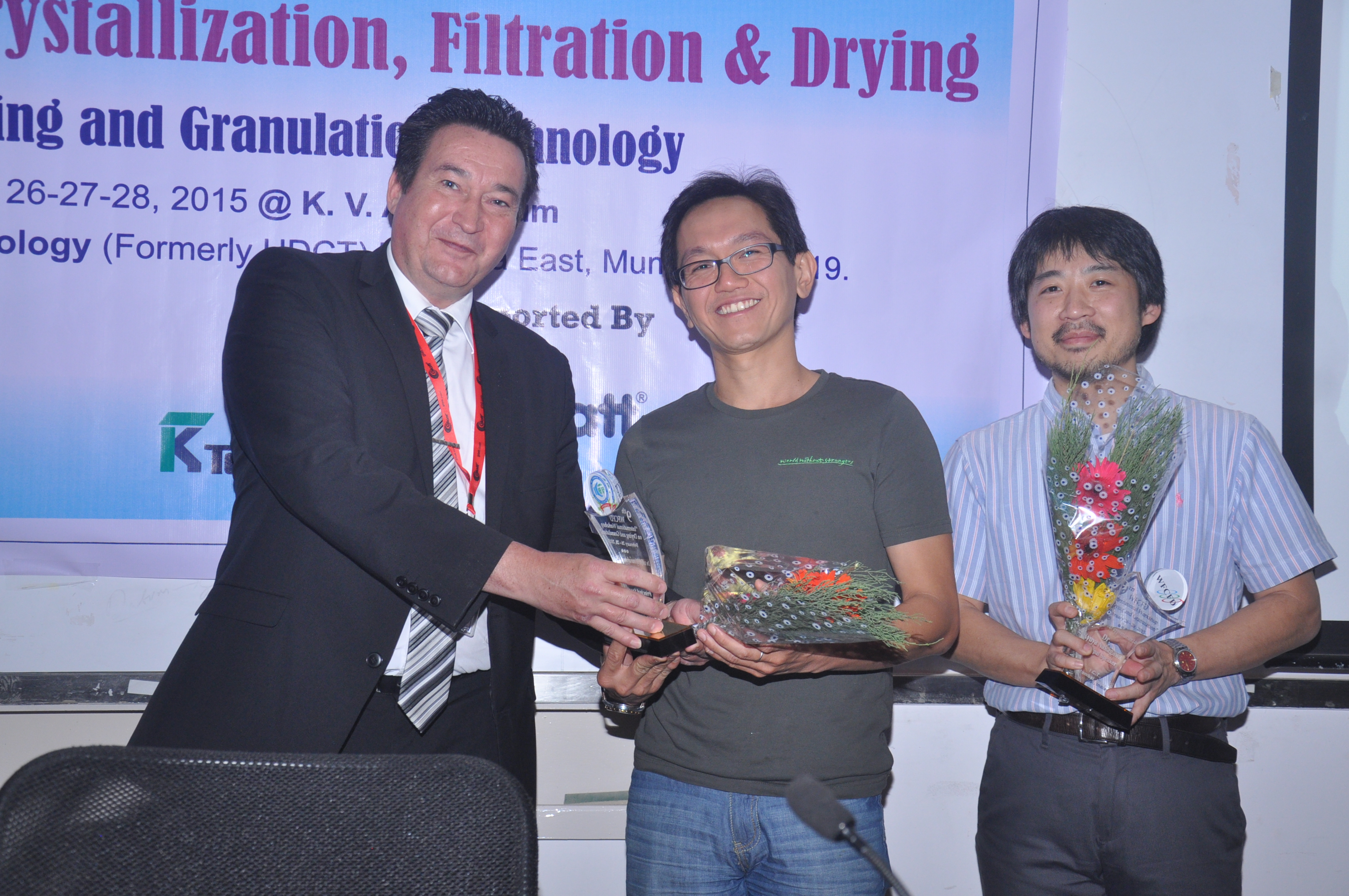
(L-R. Mr Volker Budzinski, GLATT; Prof. Meng Wai Woo, Monash University, AUSTRALIA; Dr Kyuya Nakagawa, Kyoto University, JAPAN)
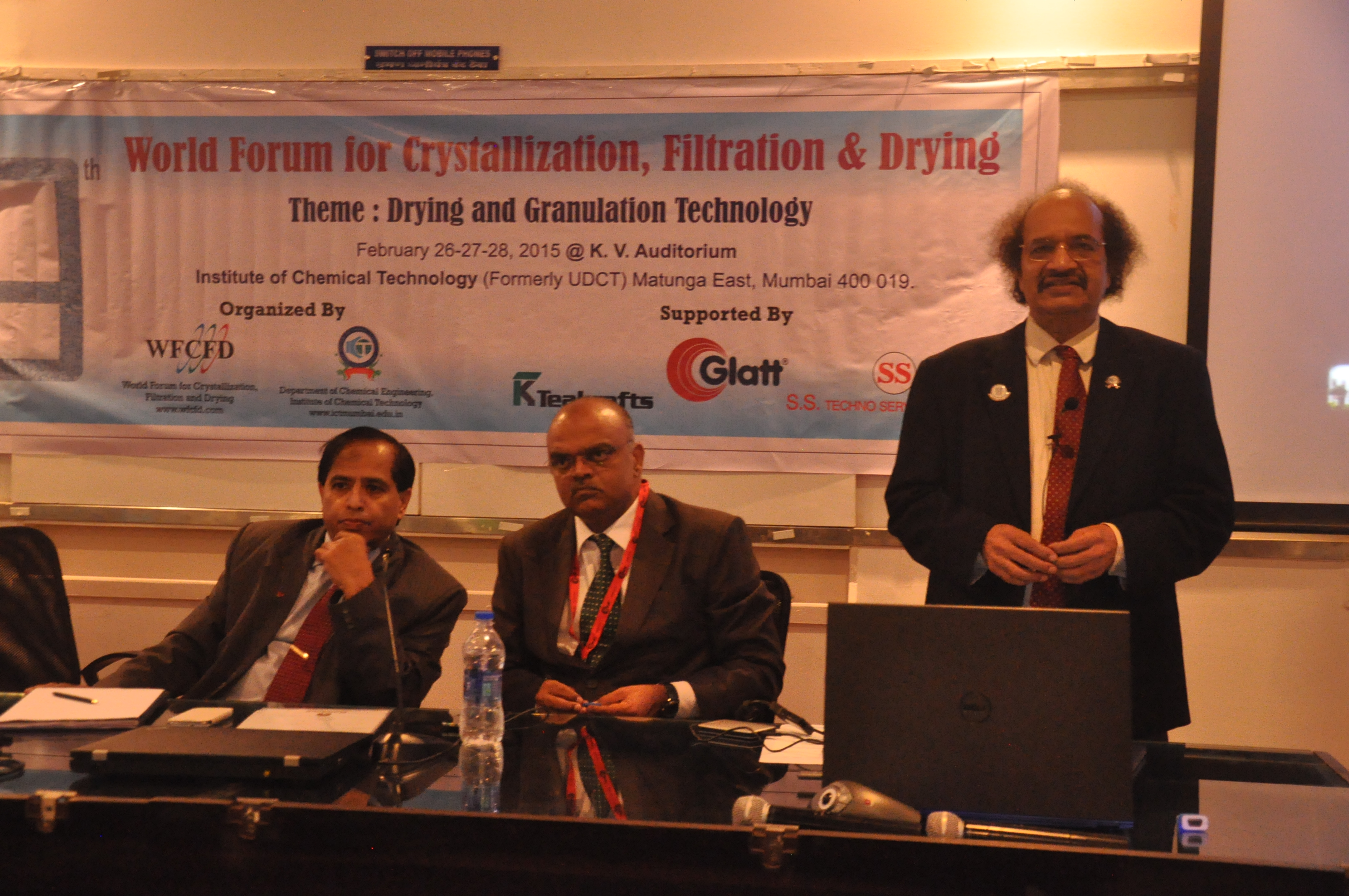
(L-R. Dr Sanjeev Katti, RELIANCE TECHNOLOGY GROUP; Prof B.N.Thorat, ICT; Prof. G.D.Yadav, Vice Chancellor, ICT )
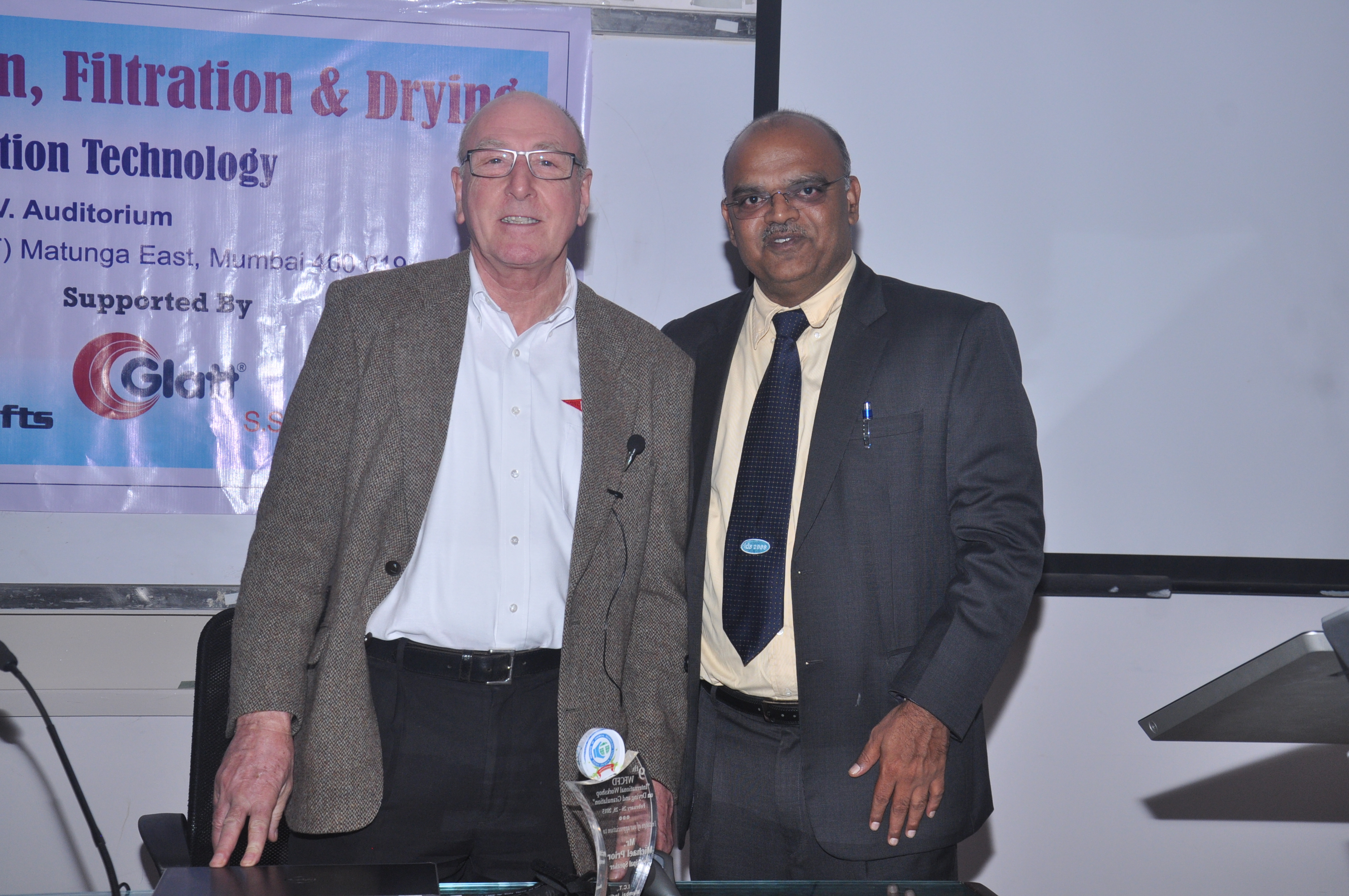
(Mr. Michael Prior, THE FITZPATRICK COMPANY and Prof. B.N.Thorat, (Professor,ICT), President WFCFD)
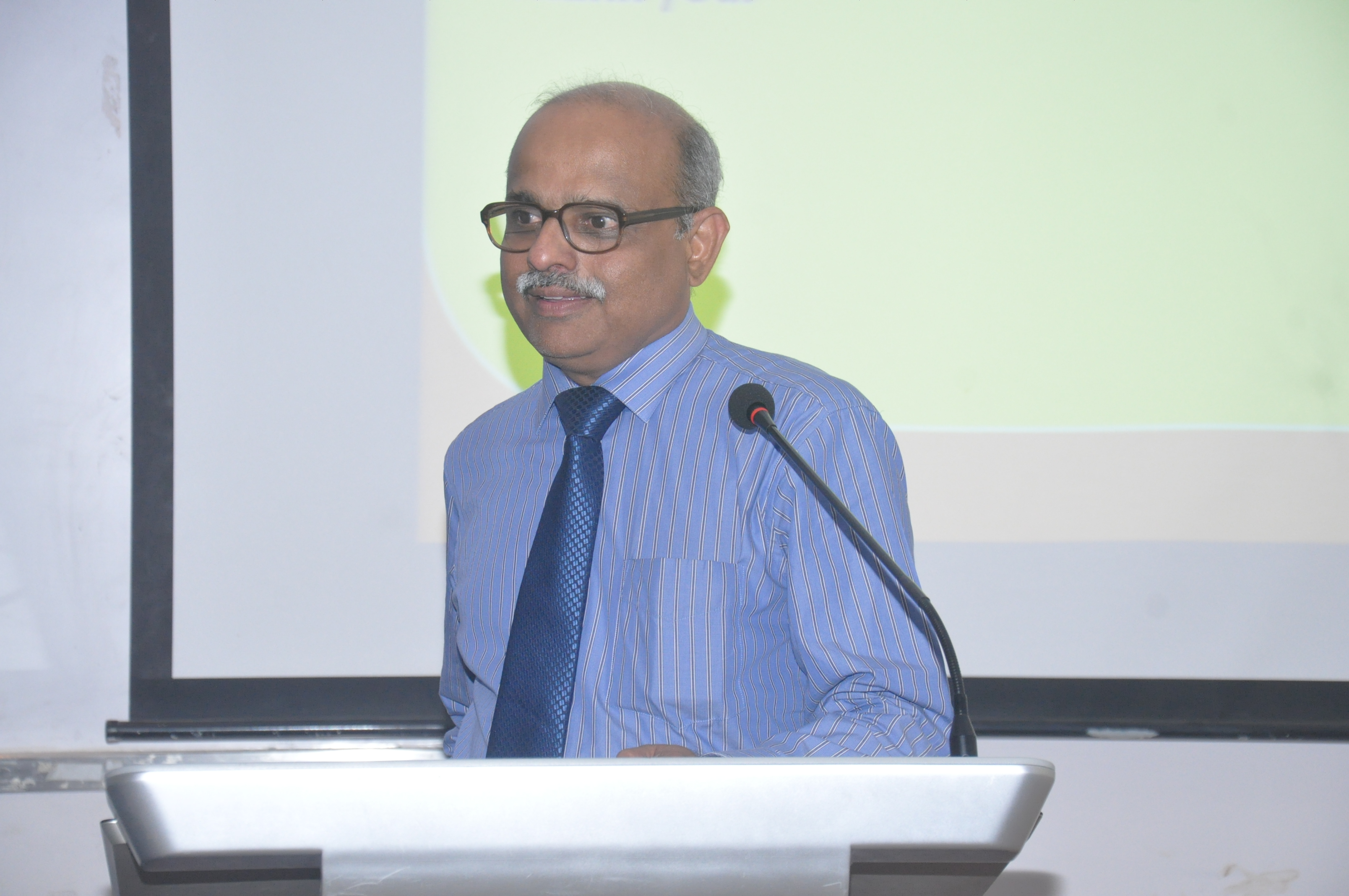
(Mr. P.B.Kulkarni, LITEL Infrared Systems Pvt. Ltd.)
|