Waste (Resource) Management of Chemical and Allied Industries
By B. N. Thorat and Poonam Vij Department of Chemical Engineering Institute of Chemical Technology, Matunga (E), Mumbai 400019. Email: bn.thorat@ictmumbai.edu.in
The International Workshop on “Waste (Resource) Management of Chemical and Allied Industries” was held on the 7th and 8th November 2014,
by World Forum for Crystallization, Filtration and Drying (WFCFD) and Institute of Chemical Technology.
The main theme of the workshop was resource management focusing on chemical aspect. It was an Industry focused
conference bringing together the current advancements and industry experts to share their views on various techniques of Resource Management,
the current scenario and the future roadmap.
The Main aim and objective of the workshop were
• Provide an interactive platform for enhancement of potential values of Waste Management
• Present real time process of Waste Management
• Illustrate examples as solutions for the current Waste Management scenario in Indian Industries
EVENT
Hosted by Professor Bhaskar N. Thorat, Institute of Chemical Technology organized the event at KV Auditorium in the ICT campus itself. The workshop featuring ten principal
speakers was attended by over 120 members from both academic as well as industrial background.
“There should be nothing like waste”, proclaimed Professor MM Sharma, while giving the plenary lecture at ICT, an Institute, which he
nurtured for over five decades by practicing what he preached. Resource management calls for the change of mindset amongst the stake holders across a wider section of industries including chemical sector. Valorising all such resource
streams should be the mantra for achieving the higher sustainability of chemical and allied industries, the need of hour, as India is inching towards adding to its capability in the manufacturing sector.
Professor Sharma, recently anointed by IChemE (UK) by establishing a global award “Career Achievement Medal” in his honour, impressed upon 120 odd delegates, which included some of the ex-directors of CSIR laboratories who attended the first of its kind of gathering on Resource Management at ICT. He started by giving a classical example of recovering elemental sulphur, ‘S’, using the catalytic claus process from H2S stream in refineries. The amine based regenerable SO2 by Scrubbing in Smelter industries to give water saturated SO2 as a by-product is another noteworthy example of converting off gases into a value added product. SO2 can be then directed to the front end of a Sulphuric acid plant for conversion to sulphuric acid. Depending on the inlet gas temperature, the emissions in the treated gas can be brought down to as low as 55 to 60 mg/Nm3. In power plant, the “Flue gas desulphurization” can be elegantly achieved by injecting either limestone slurry (CaCO3) or milk of lime, Ca(OH)2, followed by air oxidation to convert calcium sulphite into calcium sulphate dihydrate and then into valuable cement grade
hemihydrate calcium sulphate, the gypsum. Over 95% SO2 wet scrubbing efficiency has been reported in some of the new installations.
An early example of conversion of nitrobenzene to aniline using Fe as catalyst, where the spend catalyst in the form of oxides is upgraded to pigment grade. Several examples were cited by MMS, the leading chemical exponent of the globe, including the valorised products such as polyferric sulphate (PFS), a polymeric coagulant in water treatment widely used world-wide. Some of the advantages of PFS over ferric sulphate include the ability to work in low alkalinity waters, lower density, less pH depression, a faster reaction, faster settling rates and better COD/BOD removal. In similar way, the ferrous sulphate, FeSO4, obtained as a byproduct in the process TiO2 to TiSO4, can be value added to make PFS. Number of other processes doing justice to the phrase “Wealth from waste” can be thought about included, Polyaluminium chloride (PAC) from AlCl3 used as acid catalyst in FC alkylation/acylation reactions, mancozeb from the process of MnO2 to MnSO4, electrochemical process to reconvert Chromium sulphate back to Chromic, a true valorisations of otherwise environmentally sensitive Cr(VI). Copper used as a catalyst in the aryl halide coupling reactions (Ullman reaction) can be recovered to Cu(OH)2, which then can be valorised into fungicide/insecticide formulation.
In the manufacturing of Polycarbonate via phosgene route in the earlier days, NaCl, obtained as a co-product which after purification was suitably made use of in the membrane cells for caustic and chlorine industry. In the manufacturing process of soda ash, practised today in the same way, where, humungous CaCl2 is valorised in north hemisphere part of the world for winter deicing/thawing purpose. It can also be used in the establishment and maintenance of oil wells world-wide. Another classical example of yesteryears is the calcium carbide based acetylene process, where Ca(OH)2 is converted into finely precipitated CaCO3 or used elsewhere in the nearby cement industry or soda ash plant. The calcium hydroxide found the most promising use in the soda ash industries.
The bio-refractory aromatic sulphonic acid, obtained in several chemical reactions as a residue and/or co-product can be recovered via conversion to the value added aromatics such as phenol or substituted phenols.
Phosphoric acid plant generates equally large quantities of gypsum and the hemihydrate form (obtained via fluid bed or a rotary calcination) has been valorised into making of gypsum board for low cost housing projects or as such it can be used in the cement industry. Another compound in the same league is the single super phosphate, where, Sodium Silico Fluoride has been converted into cryolite (Na3AlF6), required in the Aluminium smelting industry. In the manufacture of single super phosphate fertilizer, the phosphate rock is acidulated with sulfuric acid, and the fluoride content of the rock evolves as volatile silico-fluorides. In the past, much of this volatile material was vented to the atmosphere, contributing heavily to pollution of the air and land surrounding the manufacturing site. As awareness of the pollution problem increased, scrubbers were added to strip particulate and gaseous components from the waste gases. Infact, the hudrofluorosilicic acid (H2SiF6) can be converted to high purity SiO2 which finds it ultimate use in the tyre industries. Further refining it into high grade silica has number of other high value applications such as flow agent in the making of tablets in pharma and free flowing powder/granules to arrest lumping and overcome the issue of cohesiveness of powder.
Narrating an interesting discovery of DOWTHERM, Professor Sharma gave a classical example of manufacturing of Phenol via Dow process of high pressure alkaline hydrolysis of chloro-benzene. The co-products diphenyl oxide and phenyl phenols were valorised into high temperature heat transfer media and thus DOWTHERM was born. Subsequently, in the later days, cleaner process was developed via the route of dehydration of phenol and ortho phenyl phenol from cyclohexanone.
The caustic fusion based cresols and phenolic producing companies and several other industries, generate a large quantities of sodium sulphite and sodium sulphate. The former can be reacted with sodium formate (by product in the manufacturing of pentaerythritol) yielding a value added product sodium dithionite, an important reducing agent used in dyeing industries.
HCOONa + 2SO2 + NaOH ? Na2S2O4 + H2O + CO2
On the other side, Na2SO4, obtained as a co-product in a variety of reactions including viscous rayon manufacturing, can be valorised by formulating into synthetic detergents or used in the Kraft process of paper pulping.
In classical route of manufacturing styrene, diethyl benzene is invariably obtained. Besides, recycling it, it can be converted into divinyl benzene (DVB), ubiquitously used in the making of ion exchange resins. In the same way, Phenol obtained via classical route of cumene, generates di-isopropyl benzene (DIPB) as a co-product, which again can be recycled back or valorized in to variety of products. 1,4-Diisopropylbenzene is an intermediate for the preparation of stabilizers, polymers, synthetic lubricants, hydroperoxides, and so on. The most practiced reactions of DIPB include side chain modification by oxidation, dehydrogenation, and bromination. Ring substitution reactions include nitration, sulfonation, bromination, and acetylation.
In the manufacturing of polyvinyl chloride, Ethylene dichloride is a precursor. The polychlorinated compounds based on higher chlorine content such as Carbon tetrachloride (CCl4) or Tetrachloroethane (C2Cl4), obtained by the process of Chlorolysis or poly-chlorination, has a special place amongst the chlorinated solvents. Tetrachloroethylene is an excellent solvent for organic materials. Otherwise it is volatile, highly stable, and non-flammable. For these reasons, it is widely used in dry cleaning. Usually as a mixture with other chlorocarbons, it is also used to degrease metal parts in the automotive and other metalworking industries. It appears in a few consumer products including paint strippers and spot removers.
Professor Sharma also mentions about the use of pure HOCl in the manufacturing of Epichlorohydrin via Ally Chloride, in which NaCl forms a coproduct in the second stage of alkali treatment. Valorization of maleic anhydride (MAN) obtained as a co-product in the manufacturing of Pthalic anhydride (PAN) to give fumaric acid, which is extensively used in number of applications including acidity modifier in feed industry, polyhydric alcohol and so on. Acetophenone from the by-product of phenol industry alpha methy styrene, a value addition in true sense. As is known, Acetophenone is a raw material for the synthesis of some pharmaceuticals, examples include dextropropoxyphene and phenylpropanolamine, besides use as an ingredient as fragrance.
Highlighting the typical E-factor of 20 to 100 in pharmaceutical industries, it generates typically anywhere between 10 to 20 times the so called unwanted products. Recovery of them has been in vogue in some of responsibly care companies. Typical example includes the recovery of DMF, nitro-aromatics such as Pyridine through derivatization and so on. Br2 and I2 can be recovered now in the best possible economic way and a large number of industries are practising it inhouse rather than hiring the spent processors. With the advent of nano-filtration based on ceramics or polymeric materials, it is now possible to recover several compounds and certainly those in the range of 250 nm and above.
Champion himself by miles, Professor M. M. Sharma exudes the confidence amongst the chemists, chemical engineers alike and ask the 120 odd delegates to vouch for the guaranteed 100,000 crore business in valorisation and be a stakeholder in making a chemical industry more sustainable by adopting the 4 ‘R’ principles of Reduce, Reuse, Recycle and finally Refuse.
The key note speech was addressed by Professor Albin Pintar, who is the Head of Laboratory for Environmental Sciences and Engineering at the National Institute of Chemistry (Ljubljana, Slovenia), and professor of chemical engineering at the Faculty of Chemistry and Chemical Technology, University of Ljubljana. Professor Pintar’s talk was based on Advanced Catalytic Process for purification of Industrial waste water, key points being Wet Air oxidation and Advanced Oxidation process for the effective mineralization of organic compounds under milder conditions using heterogeneous catalyst. He mentioned about Ru/TiO2 being stable at hydrothermal conditions, even in solutions with high salinity, not prone to deactivation due to coking of the catalyst surface, enabling complete mineralization of organic matter and active for oxidation of intermediate acetic acid. In case of photocatalytic oxidation, TiO2 nanotubes as catalyst, besides nanowires and nanofibres could be considered.
Professor Aniruddha Pandit, a senior Professor at ICT in the Department of Chemical Engineering, spoke about the room temperature technologies for the conversion of persistent organic chemicals into smaller molecules ready to be transformed into benign CO2 via aerobic oxidation. Hydrodynamic cavitation is relatively recent methodology that can be considered for treatment of effluents containing refractory pollutants. Design, development and operation optimization of hydrodynamic cavitation reactors is a promising area. There are several reports that indicate the application of hydrodynamic cavitation for wastewater treatment through novel design apart from the conventional multi-orifice devices. The scope is truly wide in treating pharmaceuticals co-products to bring down the COD substantially with higher conversion as well as energy efficiency. Professor Pandit summarized his talk by showing how reactors based on hydrodynamic cavitation show a considerable optimization possibility due to the presence of multiple pressure oscillation frequencies present as turbulent and chaotic flow.
Mr. Madhukar Naik, Managing Director of M/s Aquachem Enviro Engineers Pvt Ltd, spoke on Membrane Biorecator (MBR) and Fixed & Moving Bed Bioreactor (MBBR). With more than 30 years in the field, Aquachem is a leader in wastewater treatment and has completed, more than 6 CETP’S, 25+ Sewage Treatment Plants and more than 250 ETP’s. He also mentioned about several competitive biological processes including Submerged Aerobic Fixed Film (SAFF), Fluidized Aerobic Bioreactor System (FAB) and Sequential Batch Reactor Systems and compared their performance in terms of techno-economic factors. Mr. Naik also stressed upon the advanced high rate waste water treatment technology using MBBR giving rise to high treatment efficiency, low capital, operations and maintenance cost. He also enumerated other essential factors such as ability of MBBR to handle varying loadings from different sources. His mantra has been Simple, Reliable, Robust and Trouble free operation. Membrane bioreactors are capable of biological treatment along with disinfection, reduced sludge and complete control over sludge age (an important parameter that is often neglected). MBR gives efficient low pressure filtration without fouling, smaller foot print and therefore a compact unit, robust system of high MLSS (>10,000 mg/l) and importantly now sludge bulking.
Professor V.V.Mahajani, an Emeritus Professor of Chemical Engineering Institute of Chemical Technology spoke on Conservation of Water and Energy via Wet Air Oxidation (WAO). Being from an academic background with hands on experience as a project manager, Professor Mahajani explained the detail theory behind all the Oxidation processes ie Hydroxyl Radicals formation mechanism, use of Fenton chemistry and ozonation. The advantages and limitations of the various processes were discussed as well. Water and energy are becoming more and more important to chemical process industries due to limited sources and therefore the proper treatment is imminent for the sustainability of the chemical and allied sector. Professor Mahajani talked about the homogeneous as well as heterogeneous catalysts used in WAO and the cost implications. WAO can handle up to COD up to 50% (10,000 to 50,000 mg/l) and can handle toxic chemcials such as cyanide, sulfides, chlorophenols, amines, high TDS streams and metals. Total mineralization of waste, possible recovery of Acetic acid and similar compounds post WAO are some of the salient features of the process, claimed Professor Mahajani.
Dr. Sukumar Devotta, the former Director of NEERI, Nagpur, has done pioneering research in the field of energy and environment. Dr. Devotta has contributed for over a decade to the issues on environmental protection. He has been deeply involved in the issue of CFC replacement both nationally and internationally particularly for the refrigeration sector. Dr. Devotta talked about the resources handling challenges in chemical and allied industries and stressed upon the use of green solvents and green processes.
Dr. Kalyan Raman, Doctorate in Environmental Biotechnology from NEERI, Nagpur India, is presently working as Divisional Manager & Head, Centre of Excellence (Biotechnology) and Water & Wastewater Treatment Technologies in Research, Technology and Innovation Centre (RTIC) at Thermax Ltd. Dr Raman presented the Recent Trends in Water & Waste Water Treatment Technologies. The talk was based on the India Centric Solutions focusing on the Membrane distillation technology (Memstill) that uses low cost waste heat. Dr. Raman spoke about the “Forward osmosis (FO) technology for water treatment”, defined as the net movement of water across a selectively permeable membrane driven by a difference in osmotic pressure across the membrane. A selectively permeable membrane allows passage of water rejecting the solute molecules or ions. He claims that Forward osmosis has high rejection of wide range of contaminants having a lower membrane fouling propensity than pressure-driven membrane processes (RO). The main advantages of using FO are that it operates at low or no hydraulic pressures. Several interesting state of the art innovative suggestions came from him including the Nano-coating with anti-microbial capabilities to reduce the bio-fouling of membranes, mixed metal oxide nano-structured materials for photo-catalytic oxidation of organics, development of porous polymer based UF with nano-coating to enhance flux and resistance to contamination.
Mr Shripad Khatav, a technocrat turned entrepreneur, started S.S. Techno Pvt Ltd in the year 2000. He attributes the success to strong work force, of which more than 50 per cent are engineers. Increasing industrialization already started attracting the attention of environmentalists and Mr. Khatav – a foresighted technocrat - saw a huge potential in the area of wastewater management. His expertise lies in multiple effect evaporators and scraped surface heat exchangers and turnkey projects for zero liquid discharge (ZLD). In several industries, ZLD has become a norm and there is no alternative but to concentrate several kgs of salts generated in pharma and other industries. Sometimes, the concentration of high boiling chemicals/solvents is a preferred route as compared to the conventional aerobic/anaerobic treatment. The distilleries are needed to adopt ZLD and convert the spent wash into a semi-solid before it is disposed either by using it as a fuel in a boiler or valorizing it as a granular fertilizer as it contains around 15% K2O on dry basis.
Dr. S. Sridhar, Scientist in the area of Membrane Separation Process at the CSIR-Indian Institute of Chemical Technology (IICT), Hyderabad spoke on “Development of Industry, Society and Academia through Chemical Engineering”. Dr. P. N Parameswaran, the Vice President (Environment) at UPL, discussed about his expertise in “Management systems post waste recovery and remediation techniques”
Dr S. Rajamani, the former director of CLRI, Chennai, is a United Nations Expert in Environment Engineering with specialization in cleaner production and environmental management in leather and agro-based industries. He gave overview about the leather industries in India and also the issues related to the Ganges pollution and the ways to overcome by adopting the newer and better leather processing technologies. He mentions about the segregated treatment and recovery of metallic chrome using a dedicated chrome recovery system. He strongly recommends the use of aerobic-membrane bioreactor sans redundant secondary clarifier for water recovery. Tamil Nadu being a water scarcity region, total recycle has become a norm rather than exception. Dr. Rajamani takes pride in being associated with several ZLD plants. The one he mentioned in his lecture was Micro-filter and MBR based system to remove colour, residual coliform, BOD and COD, the first ZLD plant installed in Leather sector in Lurca, Spain. The other notable example being RO system installed at Pallavaram, Chennai. Speaking on the need for the reduction in sludge volume, the sludge should not contain more than 20% of volatile organic matter according to the new guidelines of CPCB.
COMMENTS
“Great job! It was a nice and fruitful experience to participate at the event”
Professor Albin Pintar, Slovenia
“Fabulous and Knowledgeable Experience”
Dr. Nilambari Daripkar, Enviro Analysts and Engineering Pvt Ltd
“The Conference was nicely arranged and executed in the most disciplined manner. Prof.M.M.Sharma’s speech was as usual encouraging and many in the audience, new to UDCT were pleasantly surprise”
Mr. Madhukar Naik, Aquachem Enviro Engineers Pvt LTD
“The sessions were well blended with academics & extensive operational and field experience of the technocrats and truly we enjoyed that with great level of content feeling”
Mr. Pradeep Joshi, Green Circle InC.
SPONSORS
The workshop was made possible only with the immense support extended by our Sponsors. Our principal Sponsor was SS Techno Ltd along with Enviro Analysts and Engineering Pvt Ltd, Green Circle INC, Mahabal Enviro Engineers Pvt Ltd and Sadekar Enviro Engineers Pvt Ltd.
EXHIBITORS
Giest exhibited Zero Liquid Discharge Solutions. The motto of their company being Wealth out of Waste, they exhibited a technology platform for Profit from zero liquid discharge.
Dr. Nilambari Daripkar representing Enviro Analyst and Engineering Ltd, presented a research paper on the potency of Landfill soil, Agricultural soil and non-agricultural soil and effects on the growth of a sample plant. Hence doing justice to the title of her talk ‘Waste! Is just waste or bi product?’
Mr. Pradeep Joshi also presented a small talk on the ideas and philosophies applied at Green Circle INC.
ORGANISERS
Professor Bhaskar N Thorat.
Professor Thorat started WFCFD, a Forum which organizes international conferences/ symposia/ workshops with a focus on providing the annual event “WFCFD” since 2006.
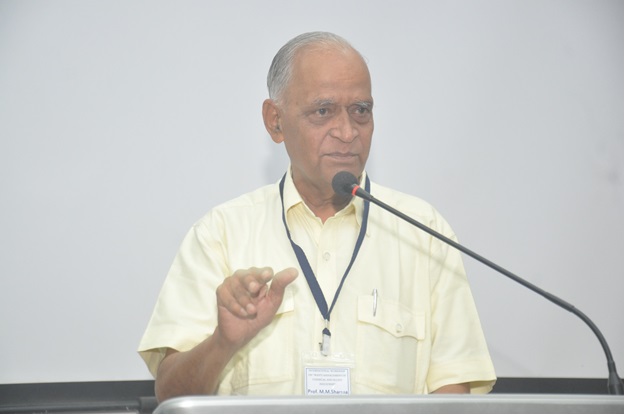
(Professor M.M.Sharma, delivering the plenary lecture at ICT)
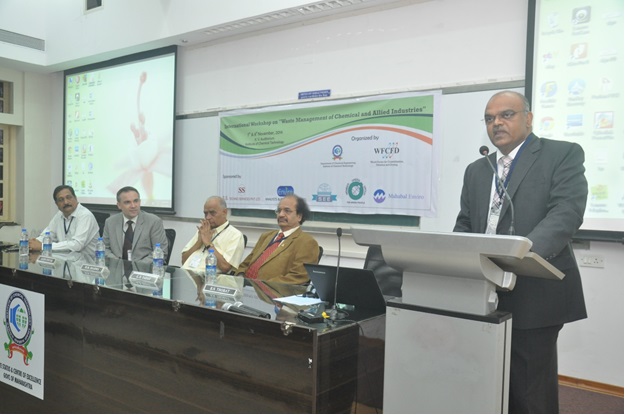
L-R (Mr.Suresh Bhosle, Prof.Albin Pintar, Prof.M.M.Sharma, Prof.G.D.Yadav, Prof. B.N.Thorat hosting the event)
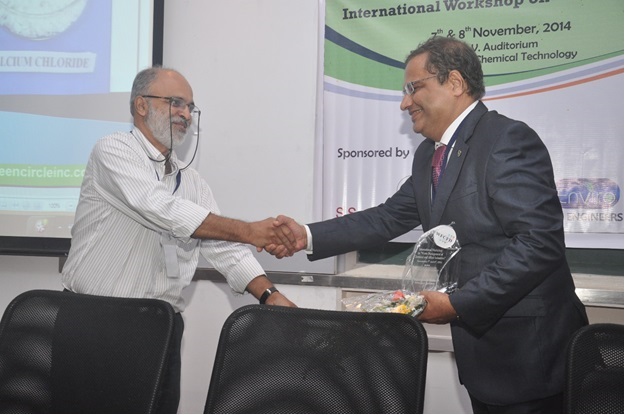
(Prof.A.B.Pandit and Mr Madhukar Naik)
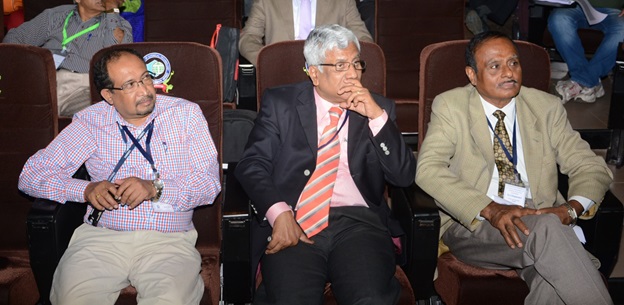
L-R. Dr. Kalyan Raman, Dr Sukumar Devotta, Dr.S.Rajamani
|